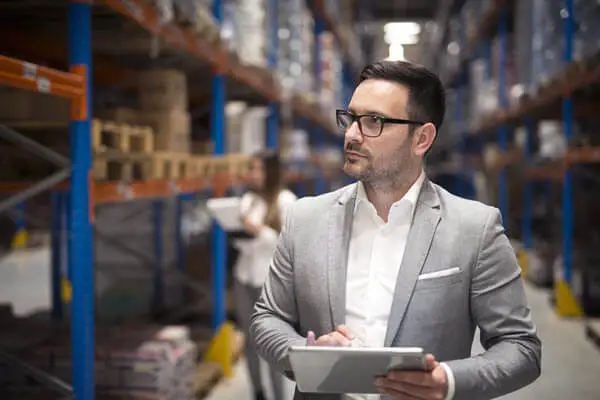
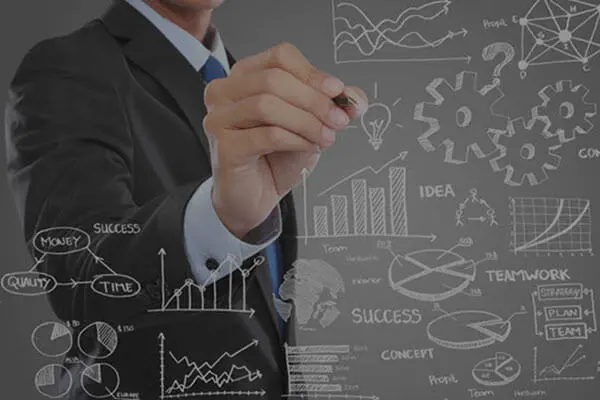
Consulting projects represent more than 80% of our engagement with clients. The value of the projects is reflected in the hands-on work within the client’s system and in achieving tangible and measurable outcomes. The best practices gained through our previous experience allow us to take a thorough assessment of current process performance and outline clear, actionable steps to achieve the desired future state and outcomes. The scope and duration of projects are tailored to the specific focus area and client requirements. Our experience has shown that periodic visits, typically one per week, deliver the best results and effective monitoring of the implementation of planned activities.
After clearly defining the project scope and strategic goals, we conduct a comprehensive analysis of process performance and identify opportunities for continuous improvement. By engaging employees in generating and implementing improvement ideas, we create the collaborative synergy that drives sustainable success.
All consulting services are fully customized to meet the client's specific needs, ensuring that the process improvements are sustained long after the project's completion. Below are some of the key focus areas commonly addressed in our projects.
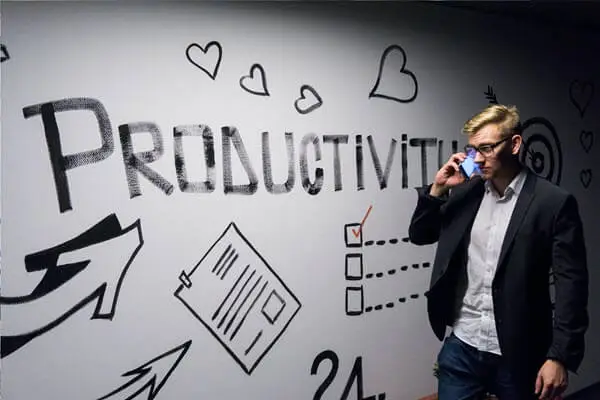
FREQUENT TOPICS AND FOCUS AREAS IN KAIZEN PROJECTS
Enhance the efficiency of manual operations, man-machine interactions, or production lines. Analyzing availability, performance, and defects leads to clear guidelines for improving efficiency.
By analyzing the root causes of scrap and applying a wide range of lean tools, we work towards achieving the Zero Defects concept.
Through the optimization of layout and the application of 5S methodology principles, a higher level of organization is achieved and waste in processes is reduced.
A detailed analysis of process structures and identification of areas for improvement, with active employee involvement, are prerequisites for eliminating waste and improving process performance.
By applying the principles of TPM (Total Productive Maintenance), the focus shifts from reactive and emergency maintenance to preventive maintenance. Involving operators in equipment maintenance through autonomous activities (lubrication, cleaning, inspection, and tightening) allows the maintenance department to focus on planned and proactive maintenance.
The application of the Kaizen methodology for structurally solving problems introduces a systematic approach to chronic issues, investigates the root causes, and eliminates them so that these problems do not recur again.
Tool changeover time represents one of the largest and most hidden potential areas for improving machine efficiency. By applying the SMED (Single Minute Exchange of Die) methodology, we systematically achieve significant reductions in changeover times.
Simply copying kaizen/lean tools will not deliver benefits or sustainable changes. Only through the development of tools by applying principles and adapting best practices to fit the system can we achieve the desired and sustainable results.
Developing a kaizen culture of continuous change through pilot projects and systematic employee involvement. Establishing kaizen routines among an increasing number of employees leads to stable and sustainable changes.
Leading groups, transferring methodology and technical skills to enable internal teams to work independently and establish sustainable changes.
Achieve additional savings by simplifying internal logistics flows and reducing transport routes. Every unnecessary meter traveled by employees or forklifts is a cost, but also a potential for savings.