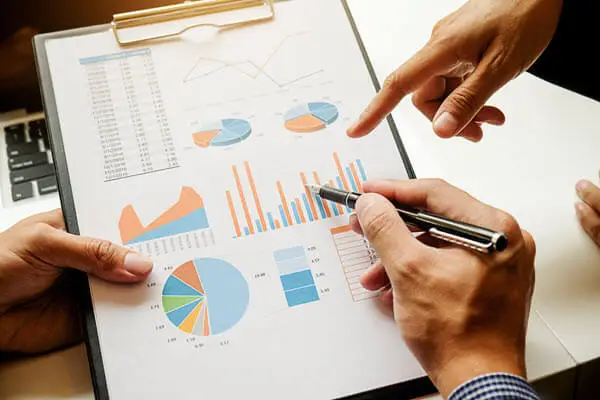
Process performance analysis involves a complete scan of the process state and identification of areas for improvement. It is most commonly conducted as the first phase of consulting projects to define priorities and enable measurable tracking of the results of actions taken. Through more than 10 specialized analyses that we conduct, it is possible to scan processes at all levels—from those that span the entire business (wall-to-wall) to the simplest, operational-level processes.
Projects without clearly defined SMART goals (Specific, Measurable, Achievable, Relevant, Time-bound) will never be completed to the mutual satisfaction of both the company and the consultant. Process performance analysis provides a clear overview of the "vital signs" of the process and determines the key performance indicators (KPIs) that we aim to improve. This approach ensures that we focus on real challenges while driving continuous, incremental improvements and providing measurable tracking of results. During the projects, we focus on transferring the methodology of performing analyses to the employees in the company so they can use it independently after the successful completion of our collaboration.
Below, you can see some of the most commonly performed process performance analyses and the results generated by their execution. The reliability of all analyses has been confirmed through past projects, and they provide an excellent way to identify areas for improvement that should be addressed during the project.
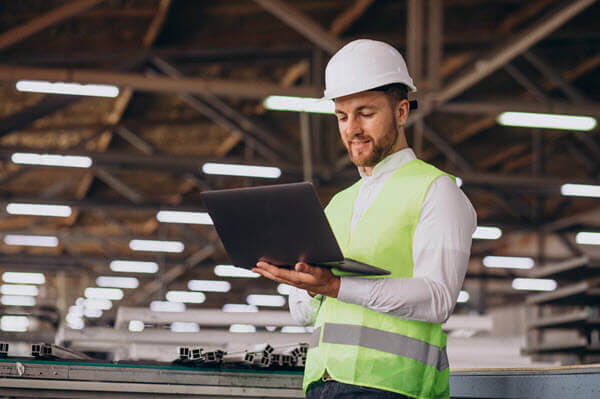
MOST COMMON PROCESS ANALYSES CONDUCTED IN PROJECTS
Value Stream Mapping (VSM) is an analysis that visually represents all material and information flows within processes and provides insight into the major challenges in achieving a smooth process flow (FLOW). It is equally applicable to both manufacturing and service industries, and employee involvement in its execution adds extra value for subsequent improvement steps.
Operation balance analysis compares the cycle times (Ct) of operations against the pace dictated by the customer through lead time (LT) and takt time (Tt). An insufficient operation balance leads to waste in waiting times between operations or excessive work-in-progress inventory, both of which directly impact the overall performance of the process. This analysis identifies the root causes of imbalances and bottlenecks in processes.
Waste analysis in processes provides a comprehensive view of the process structure, highlighting the proportion of each operation involved. For each activity—categorized into value-adding, pure waste, and support activities—a numerical value is given based on its percentage of the total process duration. This analysis clearly identifies the largest wastes and how they impact work efficiency. It is applied to processes where the main operations are carried out by humans or a combination of humans and machines.
The work environment organization analysis results in a quantified evaluation of the implementation of the 5S methodology principles and guidelines for improvement. The organization of each workstation directly impacts worker productivity, working conditions and safety.
OEE (Overall Equipment Effectiveness) represents the gold standard for tracking equipment effectiveness. This analysis is applied to production lines and is a combination of indicators related to availability, performance, and quality. It results in a clear overview and a quantified impact of factors that affect these three indicators.
TPM (Total Productive Maintenance) analysis provides an overall evaluation of the equipment maintenance process organization and results in suggestions for improvement. The focus is on preventive and autonomous maintenance to achieve savings compared to corrective and emergency maintenance, which are more commonly used in practice.
Quality challenges have proven in practice to be major drivers of significant costs, and this type of analysis gives a clear picture of the frequency, cost magnitude, and trends of defects. Statistical tools used in this analysis can reveal a large number of hidden data, making it easier to identify the root causes of issues and eliminate them.
Downtime analysis is one of the key analyses for identifying potential to increase equipment availability and overall effectiveness. Patterns and trends in downtime occurrences can help us clearly determine the direction for future actions regarding equipment management.
Inventory analysis provides data on the frequency and coefficient of variation of demand for different types of inventory, from raw materials to finished products. It serves as an excellent input parameter for inventory level optimization and the release of financial resources tied up in inventory.
Internal logistics analysis is most commonly performed using Lean tools such as Spaghetti Diagrams. The output of this analysis is an overview of the complexity, interweaving, and lengths of internal logistics routes for different types of products. It is ideal for identifying "bottlenecks" in logistics flows and finding solutions for their elimination.
SMED (Single-Minute Exchange of Die) analysis provides a complete picture of the tool change process flow and visually identifies improvement points. During past projects, potential for reducing tool change time has been identified, with reductions of up to 80%.